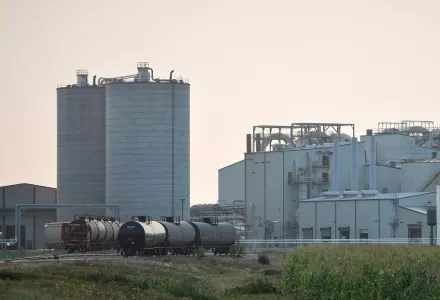
The Biden administration has set a goal of reaching net zero economy-wide greenhouse gas emissions by 2050.1 Carbon capture, utilization, and storage (CCUS)—a suite of current and emerging technologies that remove carbon dioxide emissions (CO2) from energy or industrial processes and then either sequester the carbon underground or use it for production of a variety of fuels or products2—is very likely to be a key technology on most of the plausible paths for reaching this goal.
Among various applications of the technology, CCUS in combination with natural gas powerplants can be used to provide firm baseload electricity or could serve as backup for intermittent renewable power in place of multi-day electricity storage.3 Additionally, CCUS could be used to decarbonize hard-to-electrify industrial processes4 and to provide synthetic fuels for decarbonizing nonelectric energy uses.5
The key barrier to CCUS filling these various roles and living up to its technical potential is high costs relative to current incentives: despite current U.S. government support through tax policy, CCUS is not economically competitive today in most of its applications. Unless and until it becomes so or is required by law, it will not achieve widespread deployment.
There are currently only twenty-seven operating commercial CCUS facilities worldwide, twelve of which are in the United States.6 Of the facilities in the United States, four are deployed in natural gas processing, three in ethanol production, three in fertilizer production, one in syngas production, and one in hydrogen production. All but one use the captured CO2 for enhanced oil recovery (EOR), where captured CO2 is injected into oil-containing geologic formations to ease extraction of hard-to-recover oil.7
EOR can provide a revenue source for CCUS sufficient to make a project economical in the absence of enough revenue from a carbon price or CCUS tax credit. On the other hand, low oil prices can undermine the commercial viability of projects that couple CCUS with EOR. This was the case with the Petra Nova coal power plant equipped with CCUS in Texas, which used captured CO2 for EOR but nevertheless closed in 2020.8
Altogether, CCUS facilities in the United States currently capture around 20 Mt of CO2 per year.9 This is orders of magnitude less than what is typically predicted to be needed in strategies for achieving net-zero emissions, with estimates of up to 1.8 Gt of CO2 per year captured across over 1,000 facilities for some net-zero scenarios.10 As noted, absent regulation requiring the use of CCUS, the technology needs to become more economical in order for deployment in the United States to expand significantly. That would require either decreased CCUS costs through technological innovation, or increased revenue from CCUS, such as government subsidies or the development of new, high-value uses for the captured carbon.
The main method by which the United States currently incentivizes CCUS is through the 45Q tax credit, which as of 2021 provides $36 per ton of CO2 stored in geological reservoirs or $24 per ton of CO2 used in EOR or utilized for other purposes. The credit applies to power plants that capture over 500,000 tons of CO2 per year and to industrial facilities that capture over 100,000 tons of CO2 per year.11 Facilities that capture over 25,000 tons of CO2 per year and utilize the captured CO2 for other purposes, such as production of synthetic fuels, also qualify.12 With the existing levels of the 45Q tax credit, a few CCUS facilities are starting to become economic. Between 2018 and 2020, four announced CCUS facilities specifically cited the 45Q tax credit as a key driver for the project.13
The 45Q tax credit is set to increase each year until 2026, when it will provide facilities that began construction prior to 2026 with $50 per ton of CO2 stored in geologic reservoirs and $35 per ton of CO2 used for EOR or other processes. After 2026, tax credit increases will be linked to inflation. Recently introduced bipartisan legislation, the CCUS Tax Credit Amendments Act of 2021, proposes to increase the 2026 value of the 45Q tax credit from $50 to $120 per ton CO2 for facilities that sequester CO2 and from $35 to $75 per ton CO2 for EOR facilities. Importantly, the proposed legislation allows for CCUS facilities to treat the tax credit as an overpayment of taxes and thus receive tax refunds, which is necessary because the majority of CCUS developers do not have sufficient taxable income to make use of the credit.14 The latest draft of the Build Back Better Act incorporates some of these ideas, allowing for treatment of the credit as an overpayment and raising the 2026 value of the 45Q tax credit to $85 per ton CO2 for facilities that sequester CO2 and to $60 per ton CO2 for facilities that utilize captured CO2 for EOR or other purposes.15 The Build Back Better Act would also reduce the size requirements for CCUS facilities so that electric power facilities with at least a 75% capture rate that capture more than 18,750 tons of CO2 per year, and industrial facilities that capture at least 12,500 tons of CO2 per year would qualify for the tax credit.16
Current Law17 | CCUS Tax Credit Amendments Act of 202118 | Amendments in Build Back Better Act19 | |
---|---|---|---|
2026 tax credit per ton of CO2 sequestered | $50 | $120 | $80 |
2026 tax credit per ton CO2 utilized | $35 | $75 | $60 |
Can treat credit as tax overpayment | No | Yes | Yes |
Deadline for facilities to begin construction | 2025 | 2030 | 2031 |
Capture requirements for electricity generation | ≥ 500,000 tons of CO2 per year | ≥ 500,000 tons of CO2 per year | ≥ 18,750 tons of CO2 per year; ≥ 75% capture rate |
Capture requirements for industrial facilities | ≥ 100,000 tons of CO2 per year | ≥ 100,000 tons of CO2 per year | ≥ 12,500 tons of CO2 per year |
Capture requirements for facilities with utilization | ≥ 25,000 tons of CO2 per year | ≥ 25,000 tons of CO2 per year | Same as requirements for facilities with sequestration |
Determinants of CCUS Net Costs
The unsubsidized costs of CCUS can vary dramatically, above all because CCUS encompasses multiple technologies applied to many different energy and industrial processes with different fates for the captured CO2. The cost of CO2 capture is typically the largest cost component in the CCUS process because of the energy and equipment requirements of separating CO2 from the other components of the gas leaving a facility. Across different applications, therefore, the cost of CCUS generally is higher the lower the concentration of CO2 in the gas being processed, reflecting increases in the energy needed for separation.20 CO2 capture can account for as much as 75% of the cost of the CCUS projects in applications where separation of dilute CO2 from voluminous exhaust gas is required, which includes electricity generation; cement, steel and chemical manufacturing; and oil refining.21 By contrast, in industrial applications where a high degree of CO2 separation is intrinsic to the normal process, CCUS costs are much lower; these cases include natural gas processing and ammonia production.22
Categories of CCUS Capture Technologies |
---|
Absorption capture: CO2 is absorbed into a solvent, which is typically then heated to release a concentrated stream of CO2. |
Adsorption capture: CO2 adheres to the surface of specialized materials and later is cleared off the surface to release a concentrated stream of CO2. |
Membrane capture: CO2 is captured by using membranes that selectively allow molecules to diffuse through and using differences in partial pressures to isolate CO2. |
Cryogenic separation: CO2 is separated by cooling the steam and using differences in boiling points to isolate CO2. |
Oxy-combustion: Fuel is combusted in an oxygen-rich environment which allows for a higher concentration of CO2 in the flue gas and thus easier separation. |
As with most industrial processes, CCUS costs are also impacted by economies of scale, as higher rates of total capture typically drive lower costs per ton. Current estimates show that the capital costs for CCUS typically scale with the nth power of facility size, where n ranges from 0.6 to 0.8. This non-linearity in capital costs can result in significant savings per ton of CO2 captured when moving from a smaller facility to a full-scale installation capturing millions of tons of CO2 per year.23 These cost reductions begin to diminish for facilities that capture over 0.3 million tons of CO2 per year, however, and they level off for facilities that capture more than 0.5-0.6 million tons of CO2 per year.24
In addition to the base technology and scale, how a CCUS facility is financed and operated can have a large impact on the cost of CO2 captured. The lifetime of the facility and the electricity or fuel price paid to operate the CCUS equipment are key operational parameters affecting CCUS costs. Longer facility lifetimes can lower CCUS costs by allowing repayment of the initial capital costs to be spread out over more time. Higher fuel prices increase CCUS costs by increasing the expenses needed to operate the capture equipment. The more energy intensive the facility, the more the costs are affected by fuel prices. CCUS used in conjunction with fossil-fuel-fired electricity generation is thus more sensitive to fuel prices than CCUS used with processes such as ammonia production. Key financial factors influencing CCUS costs include debt ratio, interest rate on debt, inflation rate, and tax rate. Financial factors can affect the cost of CCUS by increasing or decreasing the effective capital costs of a facility as well as how the capital costs are priced into the cost per ton of CO2 captured.
Lastly, there are costs associated with CO2 transport, compression and, if applicable, sequestration. Some net-zero pathway studies envision a nationwide CO2 pipeline network to transport captured CO2 from CCUS facilities to geologic reservoirs suitable for long term storage.25 Other studies have looked at having captured CO2 transported by truck, but analysis generally indicates pipelines to be significantly cheaper in the long run.26 CO2 compression costs may vary somewhat depending on the size of a pipeline and capabilities of the transport system.
Estimates for Current CCUS Costs
There are two main ways for calculating the costs of CCUS. The more straightforward method, generally referred to as the “cost of CO2 captured,” is derived by dividing the total incremental cost of using carbon capture at a facility by the total amount of CO2 captured. The cost of CO2 captured, however, does not account for the fact that using CCUS generally increases overall CO2 generated in a facility due to the extra energy need to run the CCUS equipment. The “cost of CO2 avoided” includes this factor by dividing the total incremental cost of using carbon capture in a facility by the difference in CO2 generated from a CCUS facility and an equivalent facility in the absence of CCUS. As there is always at least some energy used to capture, transport, and store (or utilize) CO2, the amount of CO2 avoided will always be less than the amount of CO2 captured, meaning the cost of CO2 avoided will always be more than the cost of CO2 captured.27
As there are limited CCUS facilities currently in operation, most estimates for CCUS costs come from modeling studies that apply a variety of assumptions regarding the above-mentioned controlling factors to project the capture cost per ton of CO2 for hypothetical facilities employing these different approaches. We reviewed, in depth, fifteen reports estimating the costs of CCUS applied to various industries using a variety of technologies and assumptions. Figure 1 shows the reviewed cost estimates for carbon capture along with current and proposed values for the 45Q tax credit in 2021 U.S. dollars.
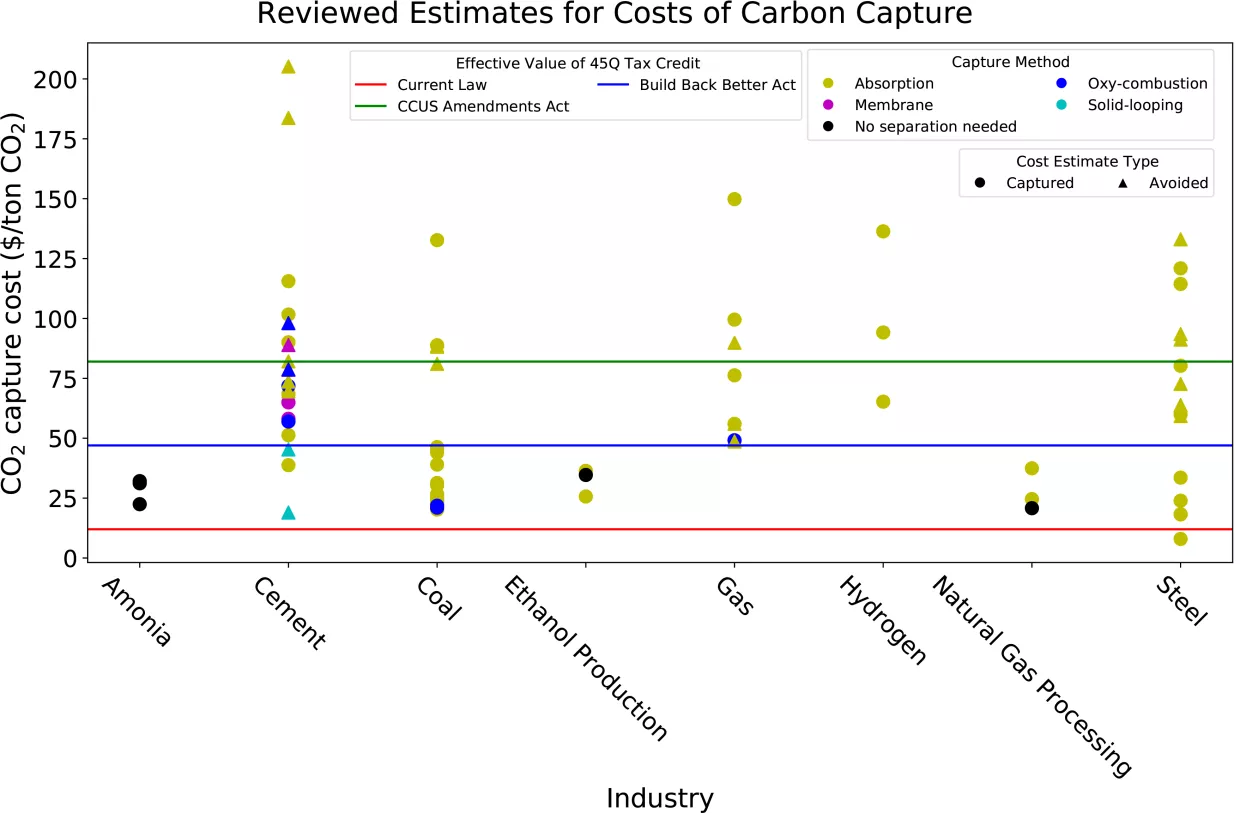
As shown in Figure 1, the estimates reviewed for the CO2 capture cost are as follows:
- Ammonia production: $22–$32 per ton
- Cement production: $19–$205 per ton
- Coal-fired power plants: $20–$132 per ton
- Ethanol production: $26–$36 per ton
- Natural gas power plants: $49–$150 per ton
- Hydrogen production: $65–$136 per ton
- Steel mills: $8–$133 per ton
Under current law, the 2026 value of the 45Q tax credit does not provide sufficient incentive to make CCUS economical for any of the reviewed cost estimates, except for one estimate of capture costs in steel production using low-efficiency capture technology. With the Build Back Better Act, the increase in the 45Q tax credit would be enough to make CCUS economical given cost estimates for ammonia production, ethanol production, natural gas processing, and for most reviewed estimates for coal power plants. The even larger increase in the 45Q tax credit proposed in the CCUS Tax Credit Amendments Act of 2021 would also provide sufficient revenue for CCUS in cement and steel production under most cost estimates, as well as for natural gas power plants given some cost estimates. Given the wide ranges in estimated costs for CCUS, even with the CCUS Tax Credit Amendments Act of 2021, CCUS would remain uneconomical under some cost estimates for cement production, coal and gas power plants, hydrogen production, and steel production.
The factors discussed previously all contribute to the large variations in estimated costs for CCUS, both within and across industries. Variations in the capture technology used within a given category can also lead to large variations in costs. For example, newer, higher-efficiency solvents can lead to lower capture costs compared to the more commonly used amine-based solvent.
Another important source of variation in the cost of CO2 captured is the energy source for running the carbon-capture equipment. Using the main power source for the facility to run the capture equipment can derate the entire facility and increase costs by reducing usable output. On the other hand, using auxiliary sources of power for the capture equipment can reduce costs but may lead to higher facility-wide emissions and large differences between the cost of CO2 captured and the cost of CO2 avoided. Utilizing waste heat to run capture equipment is another alternative which can avoid derating the facility and avoid additional emissions,31 but the potential for waste heat utilization varies across facilities and industries.
Opportunities for CCUS Cost Reductions
Although absorption-based carbon-capture technology has existed for over 40 years,32 there are still many opportunities for cost reductions in that approach as well as in some of the others. As more CCUS facilities begin operating, there is ample potential for learning by doing, as well as for CCUS costs to fall over time as different facilities try out new technologies and discover incremental efficiency improvements or other changes that can reduce costs. Both learning by doing and technological advances are generally assumed in arriving at the published long-term trajectories of CCUS costs and deployment.33
A comparison of the Boundary Dam and the newly closed Petra Nova coal-fired power plants provides a recent example of cost reductions for CCUS through application of new technologies. Although both commercial coal plants were retrofit projects using post-combustion capture via amine-based absorption, the Petra Nova plant was able to reduce the cost per ton of CO2 captured by 25-30% by using an auxiliary natural gas plant to provide steam and electricity for the CCUS equipment.34 This use of an auxiliary system to power the CCUS equipment avoids siphoning energy from the coal power plant, so the plant can maintain its original output and revenue stream, avoiding an increased cost of electricity generation.35 Similarly, waste heat can be used to power absorption-based carbon capture equipment.36 By utilizing waste heat from industrial processes, a CCUS facility could avoid derating base plant efficiency and paying for an auxiliary power source.
There are many other CCUS technologies currently in early stages that have the potential to further reduce costs. Next-generation solvents for absorption-based capture could require less energy,37 as could more efficient membranes and adsorption systems38 and new approaches for carbon capture such as calcium-looping technology.39 Also in the research and development stage are technologies for power plants based on the Allam cycle, where a CO2 stream rather than steam is used to spin a turbine, and CO2 is captured as an inherent part of the power-generation process.40
Continuing Challenges and Opportunities for CCUS
As CCUS costs remain the primary barrier to deployment, increasing the value of the 45Q tax credit as proposed in the Build Back Better Act could go a long way towards incentivizing CCUS deployment in the United States. Given CCUS cost estimates found in the literature (shown in Figure 1), the Act’s added $35 per ton of CO2 sequestered and $25 per ton of CO2 utilized should begin to make CCUS cost competitive for many facility configurations. Even so, CCUS in natural-gas-fired power plants and hydrogen production facilities is not likely to become economical at this incentive level, and many configurations for CCUS with cement and steel facilities will also likely remain uneconomical absent bigger incentives or technological breakthroughs.
Predicting technological development is always fraught with uncertainty. At an economy-wide scale, for example, a sufficiently high carbon tax would provide a strong incentive for technological innovation in CCUS across all sectors as well as incentivizing deployment of options already available. Policies that incentivize clean power generation could put CCUS at a disadvantage if the definition of clean power includes only renewable technologies and nuclear power, but they could provide additional incentives for CCUS if the governing criterion is total emissions.
An additional challenge for widespread deployment of CCUS is the transportation infrastructure needed for either utilization or sequestration. To support CCUS across the country and keep costs low, construction of a new pipeline network of around 110,000 km for carrying CO2 may be needed. Such a network might cost between $170–$230 billion to build, leading to average transport and storage costs by 2050 of between $17–$23 per ton of CO2 transported and sequestered.41 The recently signed into law Infrastructure Investment and Jobs Act has started to address this issue by establishing a new $2.1 billion loan program for CO2 pipeline construction.42 Without a pipeline network, captured CO2 transport costs might be prohibitive for facilities not near suitable geological formations or facilities for CO2 utilization.43
Acknowledgements:
This work was supported by Energy Foundation China. The authors thank Clara Galeazzi for her helpful comments.
Appendix – Studies Included in Figure 1:
Azarabadi, Habib, and Klaus S. Lackner. 2020. “Postcombustion Capture or Direct Air Capture in Decarbonizing US Natural Gas Power?” Environmental Science & Technology 54 (8): 5102–5111. https://doi.org/10.1021/acs.est.0c00161.
Biermann, Maximilian, Fredrik Normann, Filip Johnsson, and Ragnhild Skagestad. 2018. “Partial Carbon Capture by Absorption Cycle for Reduced Specific Capture Cost.” Industrial & Engineering Chemistry Research 57 (45): 15411–15422. https://doi.org/10.1021/acs.iecr.8b02074.
Cormos, Ana-Maria and Calin-Christian Cormos. 2017. “Techno-Economic Evaluations of Post-Combustion CO2 Capture from Sub- and Super-Critical Circulated Fluidised Bed Combustion (CFBC) Power Plants.” Applied Thermal Engineering 127: 106–115. https://doi.org/10.1016/j.applthermaleng.2017.08.009.
Elias, R. S., M. I. M. Wahab, and L. Fang. 2018. “Retrofitting Carbon Capture and Storage to Natural Gas-Fired Power Plants: A Real-Options Approach.” Journal of Cleaner Production 192: 722–734. https://doi.org/10.1016/j.jclepro.2018.05.019.
Garcia, Monica, and Niels Berghout. 2019. “Toward a Common Method of Cost-Review for Carbon Capture Technologies in the Industrial Sector: Cement and Iron and Steel Plants.” International Journal of Greenhouse Gas Control 87: 142–158. https://doi.org/10.1016/j.ijggc.2019.05.005.
Herron, Steve, Alexander Zoelle, and W. M. Summers. 2014. Cost of Capturing CO2 from Industrial Sources (No. DOE/NETL-2013/1602). National Energy Technology Laboratory (NETL), Pittsburgh, PA, Morgantown, WV (United States). https://doi.org/10.2172/1480985.
Kearns, David, Harry Liu, and Chris Consolli. 2021. Technology Readiness and Costs of CCS. Global CCS Institute. https://www.globalccsinstitute.com/wp-content/uploads/2021/04/CCS-Tech-and-Costs.pdf.
Leeson, D., N. Mac Dowell, N. Shah, C. Petit, and P. S. Fennell. 2017. “A Techno-Economic Analysis and Systematic Review of Carbon Capture and Storage (CCS) Applied to the Iron and Steel, Cement, Oil Refining and Pulp and Paper Industries, As Well As Other High Purity Sources.” International Journal of Greenhouse Gas Control 61: 71–84. https://doi.org/10.1016/j.ijggc.2017.03.020.
Li, Zhixin, Qinhui Wang, Mengxiang Fang, and Zhongyang Luo. 2021. “Thermodynamic and Economic Analysis of a New 600 MWe Coal-Fired Power Plant Integrated with CaO-Based Carbon Capture System.” International Journal of Greenhouse Gas Control 109: 103386. https://doi.org/10.1016/j.ijggc.2021.103386.
National Petroleum Council. 2021. “Chapter Two – CCUS Supply Chains and Economics.” In Meeting the Dual Challenge – A Roadmap to At-Scale Deployment of Carbon Capture, Use and Storage. https://dualchallenge.npc.org/files/CCUS-Chap_2-030521.pdf.
Pettinau, Alberto, Francesca Ferrara, Vittorio Tola, and Giorgio Cau. 2017. “Techno-Economic Comparison Between Different Technologies for CO2-Free Power Generation from Coal.” Applied Energy 193: 426–439. https://doi.org/10.1016/j.apenergy.2017.02.056.
Psarras, Peter, Jiajun He, Hélène Pilorgé, Noah McQueen, Alexander Jensen-Fellows, Kouroush Kian, and Jennifer Wilcox. 2020. “Cost Analysis of Carbon Capture and Sequestration from U.S. Natural Gas-Fired Power Plants.” Environmental Science & Technology 54 (10): 6272–6280. https://doi.org/10.1021/acs.est.9b06147.
van der Spek, Mijndert, Eva Sanchez Fernandez, Nils H. Eldrup, Ragnhild Skagestad, Andrea Ramirez, and André Faaij. 2017. “Unravelling Uncertainty and Variability in Early Stage Techno-Economic Assessments of Carbon Capture Technologies.” International Journal of Greenhouse Gas Control 56: 221–236. https://doi.org/10.1016/j.ijggc.2016.11.021.
Vu, Thang Toan, Young-Il Lim, Daesong Song, Tae-Young Mun, Ji-Hong Moon, Dowon Sun, et al. 2020. “Techno-Economic Analysis of Ultra-Supercritical Power Plants Using Air- and Oxy-Combustion Circulating Fluidized Bed With and Without CO2 Capture.” Energy 194: 116855. https://doi.org/10.1016/j.energy.2019.116855.
Ye, Bin, Jingjing Jiang, Yu Zhou, Junguo Liu, and Kai Wang. 2019. “Technical and Economic Analysis of Amine-Based Carbon Capture and Sequestration at Coal-Fired Power Plants.” Journal of Cleaner Production 222: 476–487. https://doi.org/10.1016/j.jclepro.2019.03.050.
[1] “FACT SHEET: President Biden Sets 2030 Greenhouse Gas Pollution Reduction Target Aimed at Creating Good-Paying Union Jobs and Securing U.S. Leadership on Clean Energy Technologies,” White House, April 2021. Retrieved September 17, 2021, from https://www.whitehouse.gov/briefing-room/statements-releases/2021/04/22/fact-sheet-president-biden-sets-2030-greenhouse-gas-pollution-reduction-target-aimed-at-creating-good-paying-union-jobs-and-securing-u-s-leadership-on-clean-energy-technologies/.
[2] IEA, CCUS in Clean Energy Transitions, Paris (France), 2020, https://www.iea.org/reports/ccus-in-clean-energy-transitions.
[3] Williams, J.H., B. Haley, F. Kahrl, J. Moore, A.D. Jones, M.S. Torn, and H. McJeon, “Pathways to Deep Decarbonization in the United States,” The U.S. Report of the Deep Decarbonization Pathways Project of the Sustainable Development Solutions Network and the Institute for Sustainable Development and International Relations, revision with technical supplement, November 16, 2015.
[4] Larson, E., C. Greig, J. Jenkins, E. Mayfield, A. Pascale, C. Zhang, J. Drossman, et al., Net-Zero America: Potential Pathways, Infrastructure, and Impacts, interim report, Princeton University, Princeton, NJ, December 15, 2020, https://netzeroamerica.princeton.edu/the-report.
[5] Ibid.
[6] “Facilities,” Global CCS Institute. Retrieved September 21, 2021, from https://co2re.co/FacilityData.
[7] Ibid.
[8] Groom, Nichola, “Problems Plagued U.S. CO2 Capture Project Before Shutdown: Document,” Reuters, August 6, 2020, https://www.reuters.com/article/us-usa-energy-carbon-capture-idUSKCN2523K8.
[9] “Facilities,” Global CCS Institute. Retrieved September 21, 2021, from https://co2re.co/FacilityData.
[10] Larson et al., 2020.
[11] Beck, Lee, The US Section 45Q Tax Credit for Carbon Oxide Sequestration: An Update, Global CCS Institute, April 2020, https://globalccsinstitute.com/wp-content/uploads/2020/04/45Q_Brief_in_template_LLB.pdf.
[12] Ibid.
[13] Beck, 2020.
[14] One Pager: CCUS Tax Credit Amendments Act of 2021. Retrieved from: https://smithsenate.app.box.com/s/yirdlay74ae3aacduz5ynfhdfe8oivks; also: IEA, Section 48A Qualifying Advanced Coal Project Credit – Policies. Retrieved September 21, 2021, from https://www.iea.org/policies/11668-section-48a-qualifying-advanced-coal-project-credit.
[15] Build Back Better Act, H.R. 5376, Rules Committee Print 117-18, November 3, 2021, https://rules.house.gov/sites/democrats.rules.house.gov/files/BILLS-117HR5376RH-RCP117-18.pdf.
[16] Ibid.
[17] 26 U.S. Code § 45Q - Credit for Carbon Oxide Sequestration, https://www.law.cornell.edu/uscode/text/26/45Q
[18] S.986 - Carbon Capture, Utilization, and Storage Tax Credit Amendments Act of 2021, https://www.congress.gov/bill/117th-congress/senate-bill/986.
[19] Build Back Better Act, H.R. 5376, Rules Committee Print 117-18, November 3, 2021.
[20] Kearns, David, Harry Liu, and Chris Consolli, Technology Readiness and Costs of CCS, Global CCS Institute, March 2021, https://www.globalccsinstitute.com/wp-content/uploads/2021/04/CCS-Tech-and-Costs.pdf.
[21] National Petroleum Council, “Chapter Two – CCUS Supply Chains and Economics,” in Meeting the Dual Challenge – A Roadmap to At-Scale Deployment of Carbon Capture, Use and Storage, 2021, https://dualchallenge.npc.org/files/CCUS-Chap_2-030521.pdf.
[22] Leeson, D., N. Mac Dowell, N. Shah, C. Petit, and P. S. Fennell, “A Techno-Economic Analysis and Systematic Review of Carbon Capture and Storage (CCS) Applied to the Iron and Steel, Cement, Oil Refining and Pulp and Paper Industries, As Well As Other High Purity Sources,” International Journal of Greenhouse Gas Control 61 (2017): 71–84, https://doi.org/10.1016/j.ijggc.2017.03.020.
[23] Kearns et al., 2021.
[24] Ibid.
[25] Larson et al., 2020.
[26] Psarras, Peter, Jiajun He, Hélène Pilorgé, Noah McQueen, Alexander Jensen-Fellows, Kouroush Kian, and Jennifer Wilcox, “Cost Analysis of Carbon Capture and Sequestration from U.S. Natural Gas-Fired Power Plants,” Environmental Science & Technology 54 (10): 6272–6280, https://doi.org/10.1021/acs.est.9b06147.
[27] IPCC, Carbon Dioxide Capture and Storage, ed. Bert Metz, Ogunlade Davidson, Heleen de Coninck, Manuela Loos, and Leo Meyer, UK: Cambridge University Press, 2005.
[28] Psarras et al., 2020.
[29] Ibid.
[30] National Academies of Sciences, Engineering, and Medicine, Negative Emissions Technologies and Reliable Sequestration: A Research Agenda, Washington, D.C.: The National Academies Press, 2019, https://doi.org/10.17226/25259.
[31] Srisang, Wayuta, Stavroula Giannaris, Corwyn Bruce, Yuewu Feng, Dominika Janowczyk, and Brent Jacobs, “Waste Heat Utilization for the Energy Requirements of a Post Combustion CO2 Capture Retrofit Study of a Cement Manufacturing Facility,” in 15th International Conference on Greenhouse Gas Control Technologies, March 2021, https://ccsknowledge.com/pub/Publications/PAPER_GHGT15_Waste_Heat_Utilization_Energy_Requirements_Capture_Retrofit_Study_Cement_Facility.pdf.
[32] National Petroleum Council, 2021.
[33] IEA, 2020.
[34] Mantripragada, Hari C., Haibo Zhai, and Edward S. Rubin, “Boundary Dam or Petra Nova – Which Is a Better Model for CCS Energy Supply?,” International Journal of Greenhouse Gas Control 82 (2019): 59–68, https://doi.org/10.1016/j.ijggc.2019.01.004.
[35] Hoffmann, Jeffrey W., Gregory A. Hackett, Eric G. Lewis, and Vincent H. Chou, “Derate Mitigation Options for Pulverized Coal Power Plant Carbon Capture Retrofits,” Energy Procedia 114 (2017): 6465–6477, https://doi.org/10.1016/j.egypro.2017.03.1783.
[36] Srisang et al., 2021.
[37] Jiang, Yuan, Paul M. Mathias, Charles J. Freeman, Joseph A. Swisher, Richard F. Zheng, Greg A. Whyatt, and David J. Heldebrant, “Techno-Economic Comparison of Various Process Configurations for Post-Combustion Carbon Capture Using a Single-Component Water-Lean Solvent,” International Journal of Greenhouse Gas Control 106: 103279, https://doi.org/10.1016/j.ijggc.2021.103279.
[38] Kearns et al., 2021.
[39] Tilak, Pooja and Mahmoud M. El-Halwagi, “Process Integration of Calcium Looping with Industrial Plants for Monetizing CO2 into Value-Added Products,” Carbon Resources Conversion 1 (2): 191–199, https://doi.org/10.1016/j.crcon.2018.07.004.
[40] Allam, Rodney, Scott Martin, Brock Forrest, Jeremy Fetvedt, Xijia Lu, David Freed, et al, “Demonstration of the Allam Cycle: An Update on the Development Status of a High Efficiency Supercritical Carbon Dioxide Power Process Employing Full Carbon Capture,” Energy Procedia 114 (2017): 5948–5966, https://doi.org/10.1016/j.egypro.2017.03.1731.
[41] Larson et al., 2020.
[42] H.R.3684 - Infrastructure Investment and Jobs Act, 117th Congress (2021-2022), https://www.congress.gov/bill/117th-congress/house-bill/3684/.
[43] Psarras et al., 2020.
Moch, Jonathan M., William Xue and John P. Holdren. “Carbon Capture, Utilization, and Storage: Technologies and Costs in the U.S. Context.” January 2022